What is Pick and Pack Fulfillment?
Pick and Pack Fulfillment: The Breakdown
Pick and pack fulfillment has revolutionized the order fulfillment process in today’s dynamic business environment. This popular method involves carefully selecting items from inventory (picking) and packaging them for shipment (packing) to fulfill customer orders.
It has become an essential strategy for businesses, enabling them to streamline logistics, deliver orders accurately, and enhance customer satisfaction. By optimizing the picking and packing processes, companies can achieve operational excellence and gain a competitive edge in the rapidly growing e-commerce market.
The Pick and Pack Process Explained
Pick-and-pack fulfillment is a highly efficient order fulfillment process utilized by businesses to deliver products swiftly and accurately to customers. This method is used as a warehouse management system and involves several key steps, each crucial in ensuring seamless order processing and shipment. Let’s explore the four main phases of the pick and pack process:
- Order Receiving
- Upon receiving customer orders from the online store, they are logged into the system for tracking and processing.
- The orders are reviewed for accuracy, and any special instructions or requirements are noted.
- Order Picking
- Warehouse personnel utilizes advanced technologies such as barcode scanning systems and handheld devices to locate and retrieve items from their designated storage locations.
- The items are carefully picked according to customer orders, ensuring accuracy and completeness.
- Order Packing
- In this step, the picked items are meticulously packaged using appropriate materials such as boxes, padding, and shipping labels.
- The packaging process aims to protect the items during transit while optimizing efficiency and minimizing waste.
- Order Shipping
- Once the items are securely packed, they are labeled with the shipping information and prepared for dispatch.
- The packages are handed over to the shipping carrier or logistics partner for timely delivery to the customers.
Following these four steps of order receiving, picking, packing, and shipping, businesses can achieve efficient and accurate order fulfillment, enhancing customer satisfaction and loyalty. As a result, the pick-and-pack process has become a cornerstone of modern logistics. This enables companies to meet the demands of e-commerce and retail operations effectively.
Pick and Pack Strategies
Pick-and-pack fulfillment services employ various strategies to optimize order fulfillment and enhance operational efficiency. These strategies are designed to meet the unique needs of different businesses, allowing them to streamline their picking and packing operations. Let’s explore four common methods used in pick and pack fulfillment:
Piece Picking:
- Piece picking and pack process work involves individually selecting items for one order at a time.
- It is ideal for smaller order volumes and offers high accuracy, but it may be time-consuming for larger orders.
- Batch Picking:
- Batch picking and pack process work involve picking multiple orders simultaneously and grouping items based on their commonalities.
- It maximizes efficiency by reducing travel time within the warehouse and is suitable for orders with similar items or attributes.
- Zone Picking:
- Zone picking and pack process work divides the warehouse into different zones. With this strategy, each picker is assigned a specific zone to fulfill orders.
- It improves productivity by reducing picker travel time and benefits larger warehouses with a wide range of products.
- Wave Picking:
- Wave picking involves dividing the picking process into waves or time intervals in the pick and pack warehouse.
- Orders are grouped and released in waves, allowing multiple pickers to work on different orders simultaneously, improving efficiency.
- Packing Strategies:
- There are also a variety of packing strategies to choose from, including cartonization, branding packaging and packing materials, and kitting.
These strategies give businesses flexibility and options to optimize their pick-and-pack operations based on order volume, product variety, and warehouse layout. By choosing the most suitable strategy, companies can streamline their fulfillment processes and meet customer expectations effectively.
Benefits of the Pick and Pack Process Work Being Outsourced
Pick-and-pack services have revolutionized how businesses handle order fulfillment, offering a range of advantages that contribute to improved operations and customer satisfaction. With its cost-effectiveness, efficiency, and ability to boost customer satisfaction, pick-and-pack services have become an essential component of modern logistics strategies. Let’s explore these benefits in more detail:
Cost-Effectiveness:
Using pick-and-pack services can save businesses a lot of money. Instead of handling order fulfillment in-house, companies can hire specialized providers to do it for them. This means they can spend money on something other than buildings, equipment, or extra employees.
Also, pick-and-pack providers often get discounts on shipping because they handle many orders, which helps reduce overall costs. This cost-effectiveness allows businesses to use their resources better and make more profit.
Efficiency:
Pick-and-pack services make the order fulfillment process smoother and more efficient. These services have trained staff and use advanced technologies like barcode scanners and systems to manage the warehouse. This helps them do things faster and with fewer mistakes.
By reducing errors, taking less time to process orders, and managing inventory better, businesses can get more done and have orders ready to ship quickly. This efficient handling of orders ensures that customers get their packages on time, which makes them happy and gives them a good shopping experience.
Boost in Customer Satisfaction:
Pick-and-pack services are essential for making customers happy. By processing orders accurately and quickly, businesses can deliver what customers want without delays or out-of-stock items. In addition, outsourced pick and pack services ensure that products are well-protected during shipping so they don’t get damaged.
Sometimes, these services even offer customized packaging, like a company’s logo or a personal note. This makes customers feel special and creates a good impression of the brand. In addition, by consistently getting orders and delivering them on time, businesses can build trust with customers, make them want to return and tell others about their positive experiences.
Picking and packing services benefit businesses that want to handle orders well without spending too much money. When companies hire experts in this field, they can save money, work better, and make customers happier. In addition, businesses can focus on what they do best while letting the experts handle the complicated task of filling orders. This is a win-win situation for both the company and its customers.
Why Choose a Pick and Pack Logistics Company to Outsource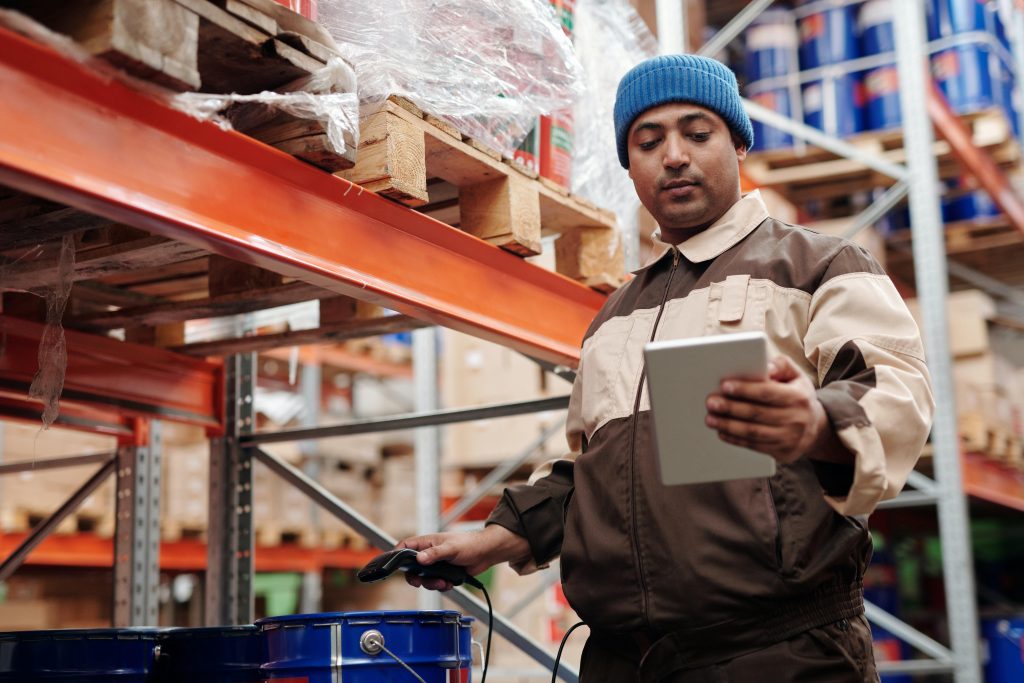
Pick-and-pack services have emerged as a game-changer in the world of order fulfillment. With their efficient processes, cost-effectiveness, and ability to boost customer satisfaction, these services have become an invaluable asset for businesses.
Businesses can streamline operations, improve accuracy, and enhance the overall customer experience using specialized providers. These services allow companies to focus on core competencies and drive growth.
Embracing pick-and-pack services has become essential in the evolving e-commerce industry, enabling businesses to stay competitive and succeed. So whether you’re a small retailer or a large enterprise, consider the power of pick-and-pack services to revolutionize order fulfillment and propel your business to success.