Industrial Storage Logistics in the Mid-America Region: What is It and Why It’s Important
Industrial storage logistics requires careful planning and management to keep industrial products moving efficiently through the supply chain. Industries like manufacturing, automotive, construction, and businesses that handle heavy equipment face unique storage challenges. These companies need specialized solutions to handle the following:
- Bulky, heavy, or irregularly shaped items
- Materials that must be stored in specific environmental conditions
- Changing inventory levels based on market demand or project schedules
Because of these challenges, many businesses rely on third-party logistics (3PL) providers to create customized storage strategies. These providers help companies make the best use of storage space, improve inventory tracking, and streamline supply chain operations—without requiring major investments in their own facilities. In the Mid-America region, industrial storage logistics plays a key role in supply chain success, thanks to its central location, strong transportation network, and cost advantages.
The Role of Third-Party Logistics Providers in Industrial Storage
Tailored Storage Solutions Offered by Third-Party Logistics Providers
Third-party logistics (3PL) providers create customized storage solutions to meet a wide range of industrial storage needs. As Senior Analyst Max Freedman at Business News Daily states, “At least 90 percent of Fortune 500 companies hire at least one 3PL provider.” Rather than using a one-size-fits-all approach, these providers consider factors like inventory turnover, product type, and specific handling requirements to maximize space and improve efficiency.
Some common storage solutions include:
- Temperature-Controlled Storage: Maintains stable conditions for temperature-sensitive materials and industrial goods.
- High-Density Racking Systems: Uses automated or manual pallet racking to optimize space for different inventory sizes.
- Flexible Storage Models: Balances short-term and long-term warehousing to adjust for seasonal demand.
- Specialized Handling: Provides custom shelving and material-handling equipment for fragile or oversized items.
By offering these adaptable storage options, 3PL providers help industrial businesses expand without the need for costly infrastructure investments.
Managing Multiple Clients’ Inventory: Techniques and Challenges
Managing multi-client warehouses requires precise inventory control. Third-party logistics (3PL) providers use advanced strategies to handle large stock volumes while maintaining accuracy and efficiency.
- Warehouse Management Systems (WMS): As NetSuite explains, this system “identifies appropriate activities or tasks, monitors performance and simplifies [warehouse] operations. This system is designed for optimization of inventory, space, equipment and labor.”
- Slotting Optimization: Places high-demand items closer to loading docks to speed up retrieval times.
- Cross-Docking Operations: Reduces storage time by transferring shipments directly from inbound to outbound transportation.
- Automated Inventory Audits: Uses Radio Frequency Identification (RFID) and barcode scanning to improve stock accuracy and reduce errors.
Even with these innovations, some challenges remain, such as:
- Conducting rigorous cycle counts to maintain inventory accuracy for multiple clients.
- Allocating storage space to account for changing stock levels.
- Integrating different client inventory systems into a single tracking framework, which often requires ongoing adjustments.
Despite these obstacles, 3PL providers can simplify complex warehousing processes for industrial businesses by maintaining a strategic and well-organized approach across all operations.
The Strategic Importance of Location in Supply Chain Efficiency
How Strategic Location Affects Service Delivery and Logistics Performance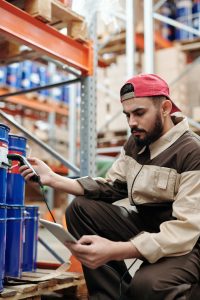
Being close to major transportation hubs has a direct impact on delivery speed and cost efficiency. Many logistics companies that work with industrial businesses choose locations near interstates, rail networks, and major ports to reduce transit times and lower freight costs.
As Andy Kirchner from DC Velocity states, “The Midwest is open for business with [supply chain] opportunities that are not available on the coasts.” Cities like Kansas City, Des Moines, and St. Louis offer key advantages for storage logistics due to their strong transportation infrastructure.
Strategic facility placement also strengthens supply chain resilience by minimizing disruptions caused by:
- Fuel price fluctuations
- Weather-related delays
- Labor shortages
This level of connectivity helps logistics providers fulfill orders faster, improving customer satisfaction and competitive positioning.
Industries such as retail, manufacturing, and e-commerce benefit from working with logistics providers in high-population areas. Shorter transport distances allow for more efficient inventory management, cutting warehousing costs while ensuring products remain available.
Because of this, Mid-America logistics companies that optimize their storage networks can quickly adapt to shifting consumer demands.
Data-Driven Site Selection for Optimized Industrial Storage
Selecting the right storage facility location requires a data-driven approach. Logistics companies use advanced tools like geographic information systems (GIS), traffic pattern studies, and freight network analytics to identify the best sites. These insights help minimize transit costs while improving operational efficiency.
- Freight Flow Analysis: Identifies key trade corridors and high-traffic transport routes.
- Market Accessibility Studies: Evaluate proximity to customer bases to shorten last-mile delivery times.
- Infrastructure Assessments: Examines road quality, fuel availability, and the reliability of transportation networks.
- Regulatory and Tax Considerations: Reviews local incentives and tax structures that affect operational costs.
Overcoming Inventory Management Challenges in Mid-America’s Industrial Storage Logistics
The Importance of Real-Time Data in Inventory Management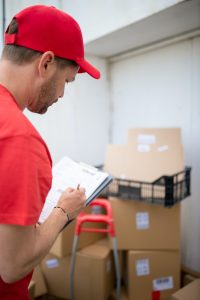
Accurate, real-time inventory data is essential for keeping supply chains running smoothly. Without it, businesses may experience:
- Stock discrepancies
- Delayed shipments
- Higher operational costs
Leading industrial storage providers in the Mid-America region use advanced data systems to monitor inventory at every stage.
Real-time data helps prevent overstock and shortages while lowering carrying costs. As Supply Chain Dive explains, “Real-time inventory visibility reduces the need for out-of-zone shipments, which cut into the profits on every order that has to be shipped from a warehouse or distribution center (DC) outside of a designated delivery area.” This level of tracking leads to fewer stockouts and improved customer satisfaction.
Real-time monitoring also strengthens decision-making. Warehouse managers can identify trends, predict demand, and streamline order fulfillment. When combined with supply chain management software, real-time data enables proactive solutions, helping to prevent disruptions before they escalate.
Deploying Information Technologies to Improve Item Tracking and Management
Technology is revolutionizing inventory management, with tools like Radio Frequency Identification (RFID) and the Internet of Things (IoT) providing greater visibility into storage logistics.
- RFID Technology: Tracks product movement in real-time, reducing manual labor and human error.
- IoT Sensors: Monitor environmental conditions such as humidity and temperature to protect sensitive goods.
- Cloud-Based Inventory Systems: Allow remote access to inventory data, enabling multiple stakeholders to make informed decisions.
Automation takes inventory control even further. As OmneelabWMS explains in a Medium article, “The utilization of advanced algorithms and machine learning ensures real-time tracking, reducing the margin of error to negligible levels. This translates into a substantial improvement in inventory accuracy, allowing logistics providers to maintain optimal stock levels and minimize the risk of overstocking or stockouts.”
By integrating these technologies, industrial storage providers in Mid-America can improve inventory management while keeping costs low. This not only reduces errors but also strengthens overall supply chain resilience.
Warehouse Automation and Technology Adoption
Latest Technologies Reshaping Industrial Storage Logistics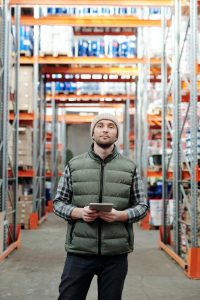
Automation is reshaping industrial storage logistics across the Mid-America region. As Logistics IQ reports, “Warehouse Automation Market is expected to reach USD 55 billion by 2030, at a Compound Annual Growth Rate (CAGR) of 15% between 2024 and 2030.” Many third-party logistics (3PL) providers are adopting advanced technologies to improve efficiency, including:
- Autonomous Mobile Robots (AMRs): Optimize warehouse navigation by adjusting routes in real-time. Unlike traditional automated guided vehicles (AGVs), AMRs do not require fixed paths, making them more flexible.
- AI-Driven Warehouse Management Systems (WMS): Predict demand changes and optimize stock levels, improving decision-making and supply chain efficiency.
- Internet of Things (IoT) Sensors: Track product locations and monitor conditions like temperature, humidity, and shock levels. This is especially important for industries handling pharmaceuticals, food storage, and high-value electronics.
These advanced technologies help reduce manual labor, minimize human errors, and streamline supply chain operations, making industrial storage more efficient than ever.
Investment in Automation for Service Enhancement and Cost Savings
Companies across the Mid-America region are making significant investments in warehouse automation. As a 2024 study by the Material Handling Institute (MHI) states, “55% of supply chain leaders are increasing their supply chain technology and innovation investments, with 88% saying they are planning to spend over $1 million.”
By adopting automation, many logistics providers are seeing key benefits, including:
- Labor Cost Reduction: Automated systems reduce dependence on manual labor, addressing rising wages and labor shortages while maintaining high productivity. Robotics handle repetitive tasks with consistent accuracy.
- Faster Order Fulfillment: Robotic picking systems speed up order processing, leading to improved customer service and fewer operational delays.
- Energy Efficiency: Smart automation optimizes energy use with features like intelligent lighting, predictive HVAC management, and automated material handling systems.
- Scalability: Modular automation solutions help businesses expand operations without major infrastructure changes. Cloud-based warehouse management systems (WMS) make it easier to increase storage capacity and integrate new technologies.
Leading logistics providers understand that combining the right automation technologies not only streamlines warehouse operations but also enhances long-term competitiveness.
Economic Impacts of Industrial Storage Logistics
How Efficient Storage Solutions Contribute to the Mid-America Region’s Economy
Industrial storage logistics is a key driver of economic growth in the Mid-America region. Efficient warehousing solutions contribute to:
- Cost Reductions: Lower operational expenses by improving storage and distribution efficiency.
- Supply Chain Performance Improvements: Streamline processes to enhance inventory turnover and speed up deliveries.
- Job Creation: Support employment opportunities across multiple industries.
These factors help logistics companies minimize waste, improve inventory management, and accelerate shipping times.
The warehousing logistics sector also plays a significant role in job growth. As the U.S. Bureau of Labor Statistics reports, “In June 2024, the transportation and warehousing industry had an employment level of 6.6 million, accounting for 5 percent of all private-sector jobs.” A substantial portion of these jobs are concentrated in the Mid-America region.
Additionally, optimized storage solutions drive regional infrastructure investments by increasing demand for transportation networks and logistics hubs.
The Relationship Between Logistics Providers and Regional Economic Growth
Logistics providers play a crucial role in shaping the economy by improving trade flow efficiency, lowering business costs, and attracting investment. Large distribution centers in cities like Kansas City, St. Louis, and Des Moines serve as economic hubs, generating revenue for local governments and supporting nearby industries.
- Job Creation: The expansion of automated warehouses and fulfillment centers has created more jobs, particularly in the industrial sector.
- Increased Trade Activity: A resilient supply chain helps manage raw material imports and distribute finished goods, reinforcing Mid-America’s role as a major logistics center.
- Infrastructure Development: The growth of industrial storage logistics drives expansions in highways, rail networks, and intermodal hubs, boosting freight movement and economic growth.
Major corporations invest in Mid-America due to its strong transportation links and cost advantages. Fortune 500 industrial companies such as:
- John Deere & Company
- Caterpillar
- General Electric
These financial benefits also extend to small and mid-sized businesses. Efficient logistics systems lower transportation costs, helping local companies reach broader markets while staying competitive. This distribution advantage strengthens the region’s commercial ecosystem and supports long-term economic growth.
Regulatory Compliance and Safety Standards
Ensuring Adherence to Regulations in Storage and Distribution
Logistics providers in the Mid-America region must follow strict regulatory guidelines set by federal agencies to ensure safety, environmental protection, and compliance.
- Occupational Safety and Health Administration (OSHA): Requires clear safety protocols for warehouse operations, including employee training, structural integrity checks, and load capacity regulations for storage racks.
- Environmental Protection Agency (EPA): Oversees the safe storage of hazardous materials to prevent contamination and pollution.
- Department of Transportation (DOT): Regulates interstate transportation, enforcing strict documentation and safety labeling requirements.
Failing to follow these federal regulations can lead to significant financial penalties. As OSHA states on its official website, “[In 2024], OSHA’s maximum penalties for serious and other-than-serious violations will increase from $15,625 per violation to $16,131 per violation. The maximum penalty for willful or repeated violations will increase from $156,259 per violation to $161,323 per violation.”
However, regulatory compliance is about more than avoiding fines—it also improves operational efficiency. Companies that follow these guidelines face fewer disruptions from inspections and legal issues, allowing them to run smoother, more reliable logistics operations.
Safety Management: From Equipment to Protocols
Workplace safety in logistics facilities relies on well-maintained equipment and clearly defined protocols. Forklifts, conveyor systems, and automated storage units must meet strict safety standards to prevent accidents.
Regular inspections and routine maintenance help ensure compliance with OSHA safety guidelines.
- Forklift Operations: Operators must have OSHA certification, with refresher courses required every three years.
- Fire Safety Measures: Facilities storing flammable materials must follow National Fire Protection Association (NFPA) guidelines.
- Material Handling: Proper labeling, weight distribution, and storage segregation help prevent hazardous incidents.
Warehouse layout also plays a key role in safety. Common hazards in industrial storage facilities include:
- Narrow aisles
- Improper shelving
- Inadequate lighting
By implementing designated zones for heavy machinery and hazardous materials, logistics providers serving industrial businesses can reduce the risk of workplace accidents.
Additionally, strong safety protocols boost workforce morale and productivity. Facilities with a well-established safety culture experience fewer disruptions, higher employee retention, and greater operational reliability in competitive logistics environments.
Cost-Effectiveness and Scalability for Industrial Storage Solutions
Balancing the Scales: Economic and Scalable Storage Strategies
Cost and scalability are key factors in the efficiency of industrial storage logistics across the Mid-America region. Businesses require customizable solutions that can adapt to:
- Fluctuations in inventory levels
- Seasonal demand
- Unexpected market shifts
Scalable storage systems provide the ability to adjust capacity as needed without excessive overhead costs.
One effective strategy is modular racking and dynamic slotting, which maximize vertical space and adapt to inventory changes, helping reduce idle storage costs. As Deskera explains, “A simple and thoughtful slotting method also greatly streamlines the process of choosing items for shipping.”
Another efficiency-boosting method is cross-docking, which minimizes the need for long-term storage by moving products quickly through distribution, lowering holding expenses.
Shared warehousing is also a cost-effective solution. Instead of each company maintaining its own facility, multiple businesses share a single warehouse, reducing operational expenses. This model is particularly helpful for smaller companies looking to optimize storage without making large capital investments.
Customized Solutions for Diverse Business Models
Adopting customizable solutions helps businesses improve cost efficiency. Automated Storage and Retrieval Systems (AS/RS) streamline industrial storage by lowering labor costs while increasing throughput. Key solutions include:
- Temperature-Controlled Storage: Maintains product integrity for sensitive industrial inventory while optimizing space.
- On-Demand Warehousing: Provides temporary expansion options for businesses with unpredictable demand cycles, eliminating long-term commitments.
- Hybrid Storage Solutions: Combines bulk storage for slow-moving products with high-density systems for frequently accessed inventory.
Logistics companies that use predictive analytics in storage planning consistently reduce costs while enhancing customer service.
Expanding Opportunities in Industrial Storage Logistics
The industrial industry plays an important role in driving economic growth, efficiency, and long-term competitiveness in the Mid-America region. By investing in advanced technology, strategic locations, and scalable storage solutions, logistics providers help businesses manage the complexities of modern supply chains.
The seamless integration of customized storage solutions, real-time inventory management, and automation not only improves cost efficiency but also strengthens business resilience and adaptability. As the region continues to expand as a major logistics hub, industrial storage logistics will remain essential in shaping a prosperous future for businesses across the country.
Take the Next Step
Are you looking for a trusted logistics provider with reliable industrial storage solutions? Partnering with a third-party logistics (3PL) company in the Mid-America region can help optimize your supply chain. Some trusthworthy providers include:
- Blue Ridge Logistics
- Mid-America Logistics LLC
- Express Logistics Inc.
All in all, working with a logistics provider that understands industrial storage can enhance efficiency, reduce costs, and improve overall operations.